Lasertube cutting: some tips
Index
- Introduction
- Design
- Cutting with tilting head (3D)
- Curved tubes and laser cutting
- Application fields
- Agrital
Introduction
The lasertube cutting machine allows the processing of all types of bar profiles. The latest generation of machines cut also shaped profiles with squared corners.
To determine the cutting capacity, we usually refer to the diagonal of the circle circumscribed to the profile.
The cutting process is the same as for sheet metal cutting.
Design a part for lasertube
If you are you able to adapt the design to the process you can maximize the result. To do that it’s necessary know the process.
In the case of laser tube cutting, the following aspects should be considered.
- Tolerances (linear, form, radial and coaxiality)
- If you need a perpendicular or inclined cut respect the surface.
- If the part must be bent later (see dedicated paragraph)
- If you need a perfect cleaned part inside.
- If you need an integrated marking to track your part.
Furthermore, some characteristics of a specific machine model are also decisive.
- The minimum length of scrapped material
- The ability to identify the position of the weld joint
- If available an integrated unit for other process (for example a tapping unit)
Tolerances
However by linear tolerances we mean the longitudinal deviation during the process: it essentially depends on the accuracy of the machine. Most of the systems today guarantee tolerances and repeatability in the order of hundredths.
The form tolerance refers to the precision with which the figure is made (the hole, the slot). It depends both by the machine (axis positioning accuracy), by the material (the dimensional deviation from the nominal section) and, also if less, by the set-up of the machine. Normally, the form error is expected in the order of a tenth of a millimeter.
Radial tolerance is very important when you need to make through holes in which respecting coaxility is essential. Laser cutting does not perform the two holes with a single positioning but rotates the profile by 180 ° after the first hole. It is therefore clear that precision is essential to obtain a coaxial tolerance in the order of a tenth of a millimeter. Unfortunately, however, the rotation can often be eccentric given above all by profiles that are not exactly linear and in any case with their dimensional tolerance. Therefore the most advanced machines have a measurement systems (by contact or optic laser reader) to realign themselves and proceed with a perfect drilling.
Cutting with tilting head
The so-called 3D lasertube are machines that allow the inclination of the cutting head. They do not to be confused with laser cutting cells (see the bent tubes paragraph). This peculiarity allows the designer to choose whether to always have cuts perpendicular to the thickness or not. The difference is more marked for thicknesses greater than 3 mm, sometimes radically changing the coupling in the subsequent phases. Let’s do some practical examples:
- With the tilting head it is possible to obtain a hole equal to that made by a drill. With the head always perpendicular, the diameter on the internal thickness will be less than that on the external diameter. The difference is more pronounced on tubes that have a round surface
- There is the possibility of making the initial inclined cuts in order to find the bevel for the next weld.
- Graded cutting can be performed as if it were a band saw or with the cut always perpendicular to the surface. The difference is especially marked for square and rectangle profiles rather than for tubes
Other peculiarities for lasertube
Cleaning inside the pipes is essential because cutting residues accumulate during processing. There are different protection systems: from the insertion of an internal core to strong suction systems that minimize the deposit inside. Depending by the application it can be a decisive aspect.
The machine also allows marking by engraving on the piece. Especially for those who work within certified production systems, identification and traceability are key points.
There are specific characteristics of the single machine model that can sometimes be decisive. For example, the most recent machines equipped with more than two spindles allow the fixed scrap to be reduced to almost zero. Therefore this means a significant savings, especially in the case of stainless steel or aluminum alloys.
Sometimes it’s required to place the weld seam in a specific position. In this case, many machines have an infrared camera (or other system) that detects the bead and orients the tube automatically.
The last important feature present in some models is a tapping unit that allows the threading to be integrated into the machining cycle. In this way, a finished product is obtained without further rework, reducing processing costs.
Bent tubes and laser cutting
This article focuses on laser processing of tubes or bar profiles. Making holes or notches on pieces that will subsequently have to be bent is sometimes not possible.
The problems are different but mainly two:
- the ability to maintain the prescribed tolerances after bending, typically center distances between holes.
- the presence of holes near or in the area to be bent leads to inevitable deformations of the same holes.
Therefore, for the aforementioned cases, the technological cycle is substantially reversed. First bent the piece and then drill it as required. Unfortunately it is an operation that raises production costs.
However, lasertube cutting is no longer the ideal machine but a robotic laser cutting cell is needed. It can be considered the big sister since the tube laser cutting machines inherit the 3D and tilt head technology from the cells.
The cells are born as a response to the need for drilling and trimming of cold forged pieces. The first applications were for automotive parts such as doors, hoods and other parts of the bodywork.
A cell requires the creation of one or more specific equipment to block the piece during processing. Furthermore, the cycle time is less rapid than bar cutting. For these reasons the costs with this process are higher but sometimes necessary.
Alternatives to processing with a laser cell can be machining centers or a robot equipped with plasma cutting units. However, even in these cases, fixing equipment is always needed and the cycle times are not comparable to the tube laser.
Alternatives
In addition to the laser cell described above, there are other alternatives for processing tubes.
- Cold forging
- Cutting with a band saw or disc and with subsequent drilling with a drill or milling cutter,
- Integrated cutting lines with punching and milling
Application fields
The use of laser tube cutting finds application space in various sectors. Below, with a short photo gallery divided by sectors, we present some possible fields of application.
- Architecture and construction with the construction of canopies, facades and canopies.
- Metalworking with the construction of frames and pylons
- Oil & Gas with heat exchangers and tanks
- Furniture with, for example, frames for chairs and tables
Agrital: our know-how
Agrital has been using this technology since 2003. It was among the first companies in Italy to have bet on this type of technology and today it can offer its customers a solid know-how on this type of processing.
We deliver across all Europe, also in small and medium batches.
Feel free to contact us for any technical questions or for a sales inquiry.
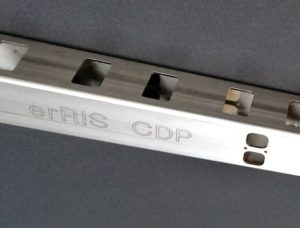
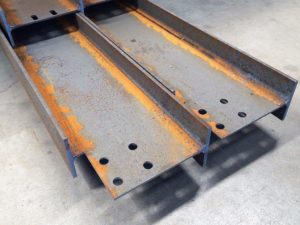
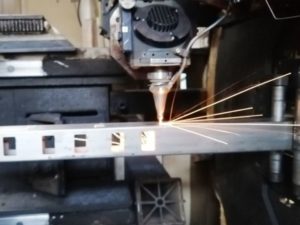
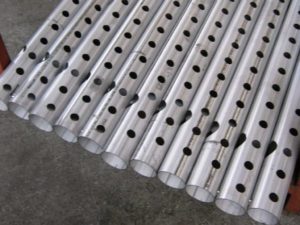
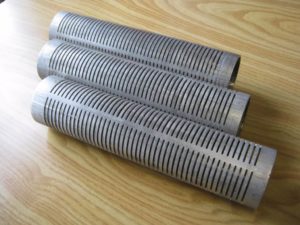
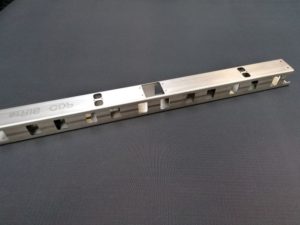