3D tube laser cutting
Tube laser cutting is a specific machine for cutting tubes, square and rectangular tubes, plates and shaped profiles. Ultimately, the process is the same as the more common sheet metal laser cutting but the layout of the machine is designed to handle bars (rods) and not flat sheets.
We currently have 2 specific systems for tube laser cutting, one of which has a 3D cutting head (i.e. tiltable).
We have been using laser technology for tubes since 2003, the year of the first installation. Therefore, we were among the first in Italy to believe in this technology. We currently have these machines:
- The first is a machine installed in 2014, built by the Japanese company Mazak. It is equipped with a 2.5 kw Panasonic CO2 resonator. It works with diameters up to 220 mm and has a tiltable head.
- The second machine was installed in 2023, produced by BLM Adige. It is equipped with a 3 kw fiber resonator. It works with diameters up to 156 mm in diameter.
The systems can work tubes from a minimum diameter of 20 mm to a maximum of 220 mm (8 inches). All square profiles, rectangles and open profiles such as beams whose largest diagonal is equal to or less than 220 mm can also be worked.
Finally, with the laser tube we can cut different types of materials: steel, stainless steel and aluminum alloys.
Peculiar technical aspects for tube laser
This tube laser cutter stands out for several unique technical aspects in its category:
- A cutting head tiltable up to 45 ° which means being able to perform 3D cuts thanks to the integration with the other axes of the machine.
- The ability to work bars up to 8 meters. Furthermore, for pieces over one meter in length, the fixed material deviation is zero. This is a peculiar trait that sets us apart from the competition.
- A unit of measurement for verifying the linearity of the bar and therefore guaranteeing the coaxiality of the holes on the opposite faces of the piece.
- An integrated tapping unit to be able not only to drill but also to thread the piece without having to make expensive manual restarts of the same.
- An optical sensor to identify the position of the welding bead and therefore be able to automatically decide which faces to work by correctly orienting the piece.
- Total integration with the company IT system to reduce start-up and machine downtime. The diagnosis is carried out remotely to define the scheduled maintenance intervals with the parent company. In the end it is a machine ready for industry 4.0
For other tips concerning the lasertube please click here.
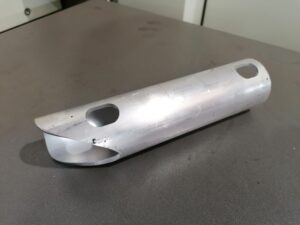
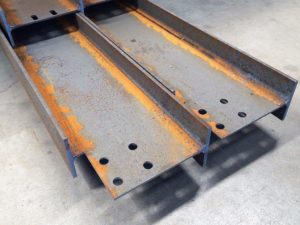
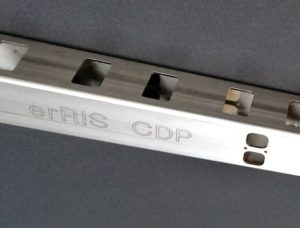
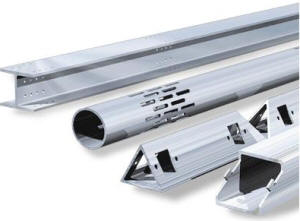
Agrital
We are a metalworking company active since 1972. We started in the agricultural mechanization sector with the construction of tractor cabins.
Today, thanks to a staff of over 50 people, we are present in various product sectors, mainly producing driver’s cabins, hydraulic tanks and hoods. In addition to having been the forerunners since 2003 in laser tube and sheet metal processing.